Traceability
Full traceability of production process
We disclose the traceability of all our products on a dedicated website.
By scanning the QR code attached to our products, you can view the process from the cotton's origin to shipment.
In an age when corporate transparency and reliability are in high demand, we started this initiative out of our desire to be faithful to society.
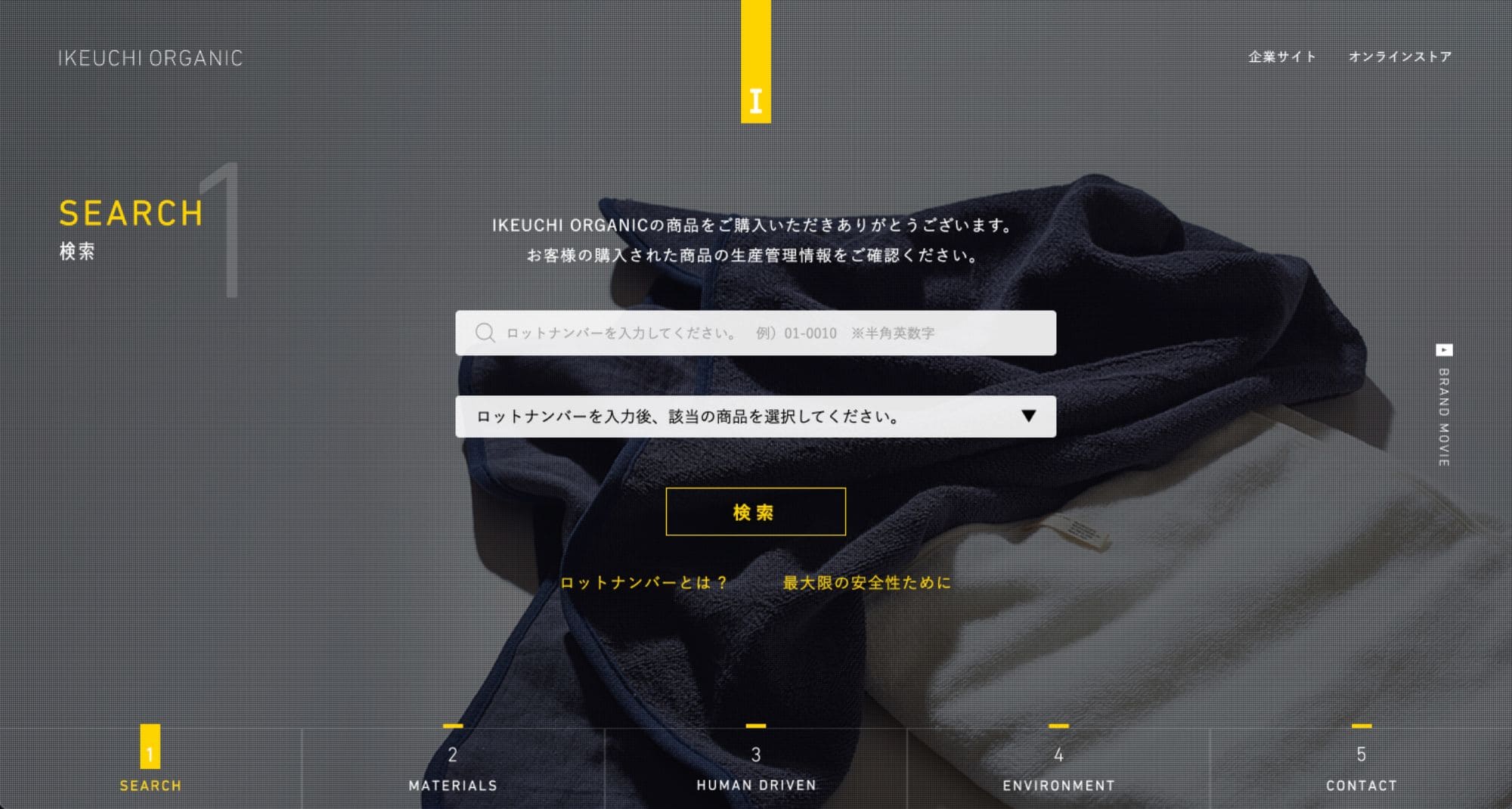
How organic towels are made
The process of making a single towel involves many steps, starting with the cultivation of cotton, spinning the cotton into yarn, weaving the towel from the yarn, and dyeing it.
In order to provide our customers with organic towels that are safe for babies to put in their mouths
IKEUCHI ORGANIC has established strict screening and quality standards in these processes.
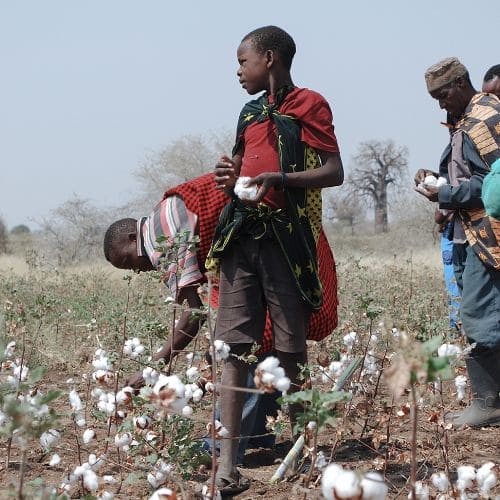
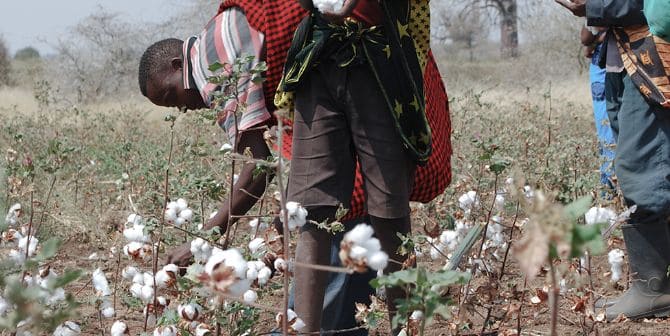
Cotton Cultivation
Cotton grown using organic farming methods
The production process of IKEUCHI ORGANIC towels begins with growing organic cotton, the raw material for the towels. bioRe PROJECT (REMEI, Switzerland) manages the organic cotton cultivation by local farmers. Seeds sown in spring grow to a height of about 60 cm, with branches and leaves extending in all directions, and lemon-colored flowers bloom in summer.
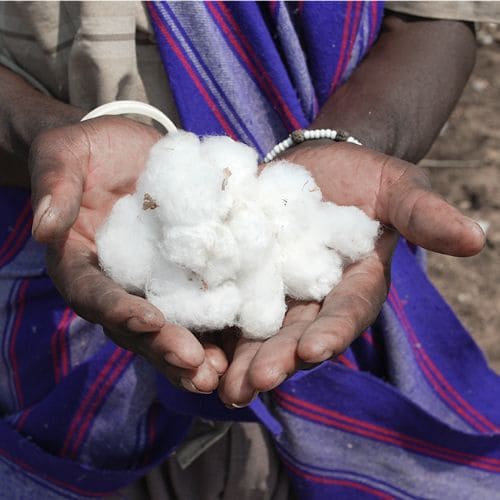
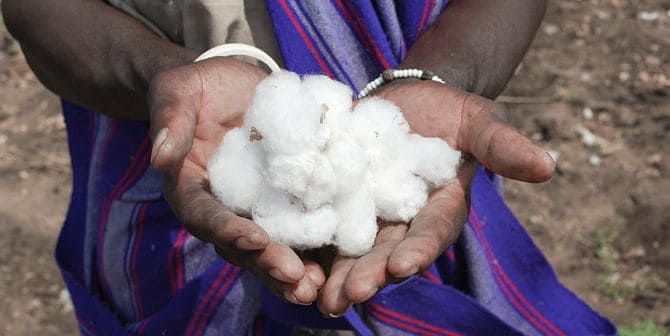
Cotton Harvest
Cotton is carefully handpicked one by one.
When the cotton balls burst and the surrounding leaves die naturally, it is a signal that the cotton is ready to be harvested. No defoliant is used. The farmer's family members work together to hand-pick and harvest the many cotton plants that have plumped up all over the field.
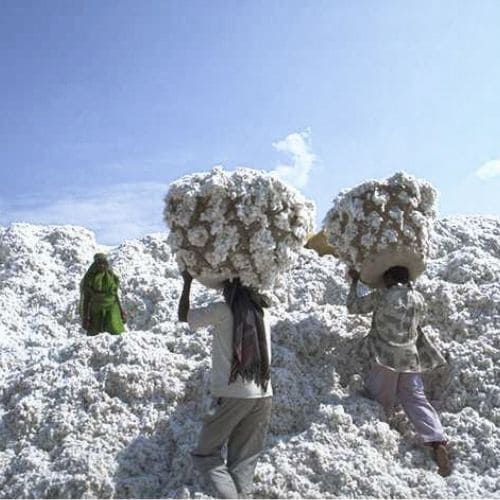
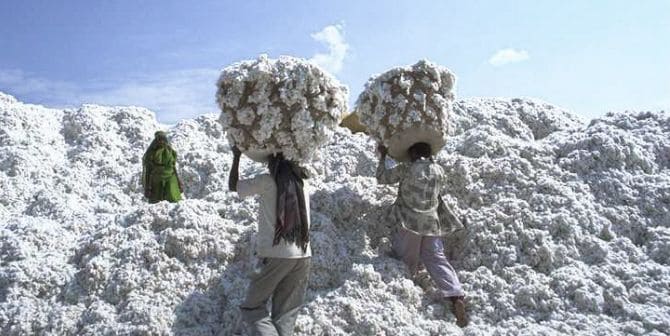
Cotton accumulation
Creating Fair Trade
Premium Price
Cotton harvested by each farmer is collected and weighed at a collection point. The bioRe PROJECT purchases this cotton at a 15% premium to the market price of organic cotton. This premium is based on the average price of cotton over the past five years and is determined with farmer representatives.
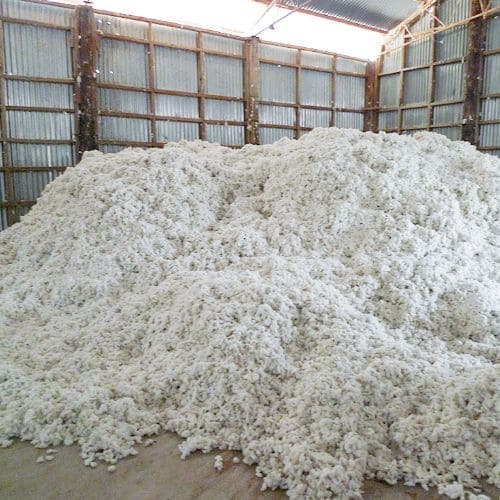

Ginning (ginning)
Removing excess seed
Once purchased, the cotton is transported to a certified organic mill. At the ginning mill, the cotton is separated into fibers and seeds by rollers. A cotton ball contains about 15 to 30 seeds, which is about 2/3 of the entire cotton ball in terms of weight. 90 kg of cotton is harvested, about 60 kg are seeds, and the remaining 30 kg are cotton fiber.
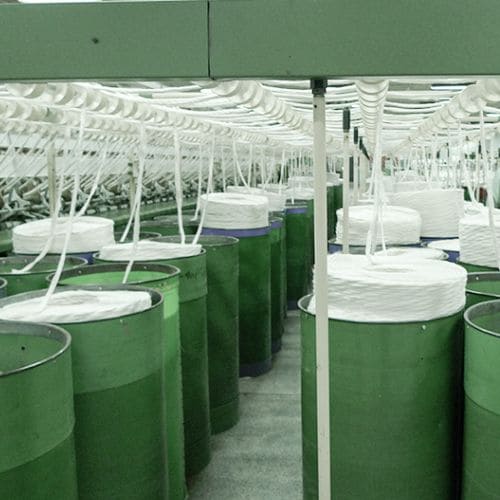
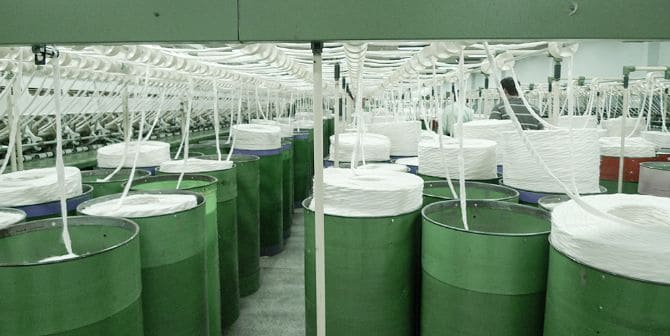
Spinning
Blending → kneading → rough spinning → spinning
Cotton of slightly different textures grown by farmers in their respective fields is mixed (blending) to achieve a uniform quality, and after removing small particles and short fibers, it is stretched to a certain thickness (kneading). After this, the yarn is stretched to a certain thickness (kneaded strips). After further stretching with light twisting (coarse spinning), it is processed into yarn with a specified twist and thickness in the spinning process.

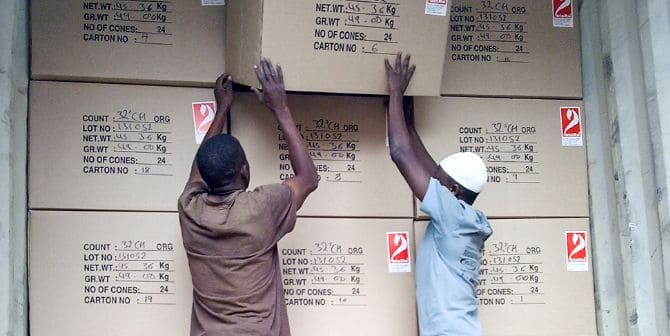
Transportation
From far away
Slowly transported by ship
The yarn is wound into tubes called cones, packed in containers, and shipped to Japan from ports in Tanzania and India, where the yarn is produced. After being transshipped to other Asian countries (Singapore and South Korea), the yarn arrives at the port of Imabari, where IKEUCHI ORGANIC is located, in about 4 to 6 weeks.
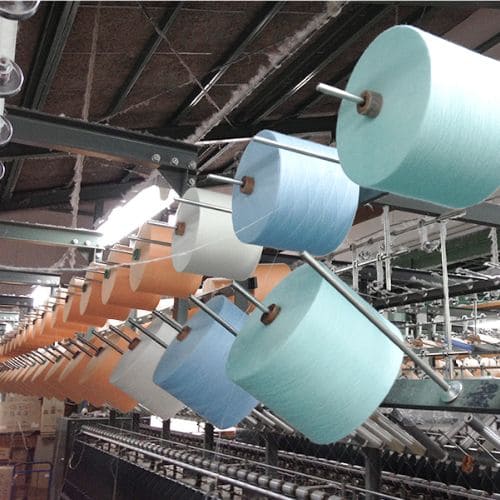
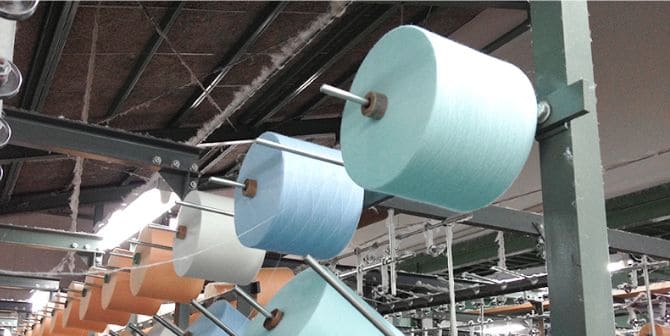
Yarn Processing
To improve the texture of towels
A twist to improve the texture of towels
The raw yarn is in its raw state when it arrives in Japan. For example, when twisting single yarns in their raw state into two yarns (twin yarns), a yarn twisting process is performed. After this process, the yarn, which had been wound around a conical tube called a cone, is rewound into cylindrical cheese rolls for easier processing.
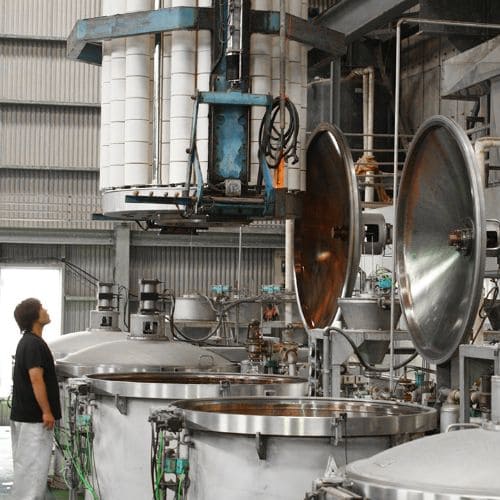
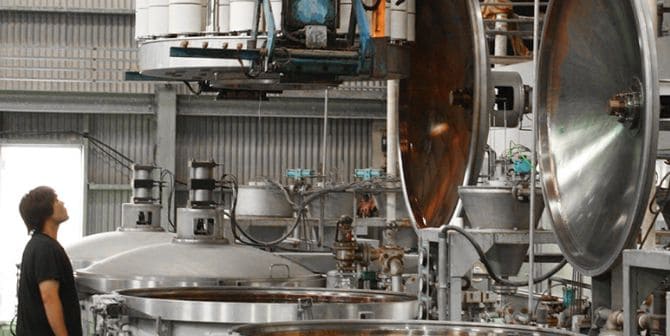
Refining, bleaching, and gluing
Cotton is actually
As it is, cotton repels water.
In order to improve cotton's natural water absorbency, impurities and oils contained in the yarn are removed (scouring and bleaching). IKEUCHI ORGANIC uses starch paste to reduce environmental impact.
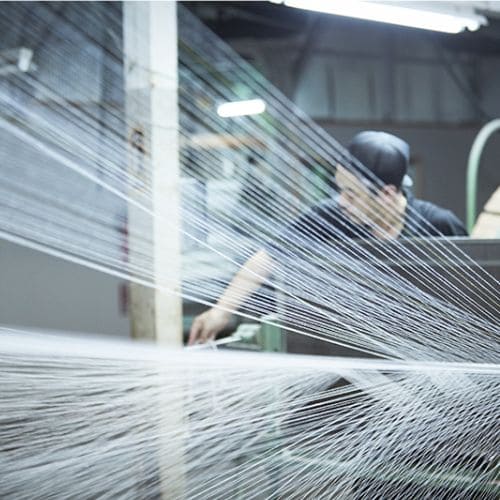
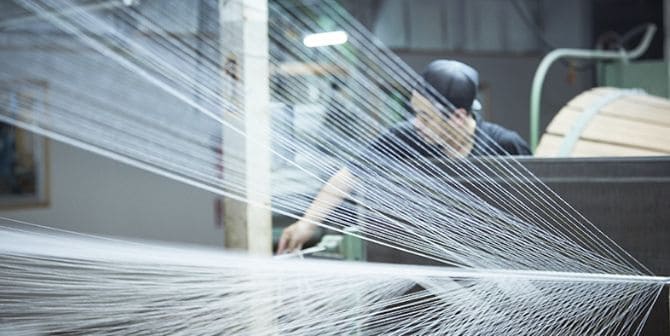
Stitching
Carefully and precisely
arranged one by one.
After processing, the threads are wound onto wooden tubes and delivered to IKEUCHI ORGANIC's main factory for the first time. The yarns are placed in a machine called a creel, which can hold approximately 500 yarns, and are wound onto a large "beam," which is used for the weaving machine. The yarns are laid out one by one according to a blueprint, and then wound under moderate tension to create the beam, which is the basis for weaving towels with a variety of expressions.
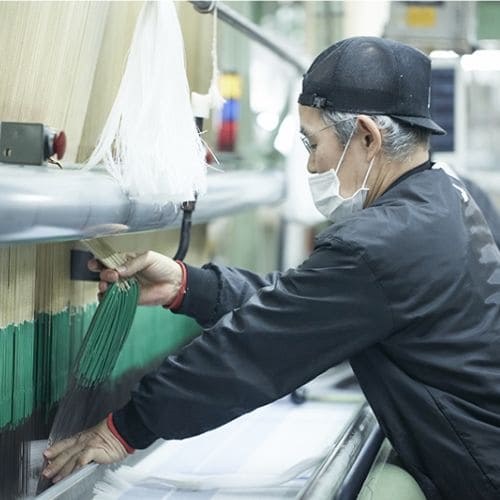
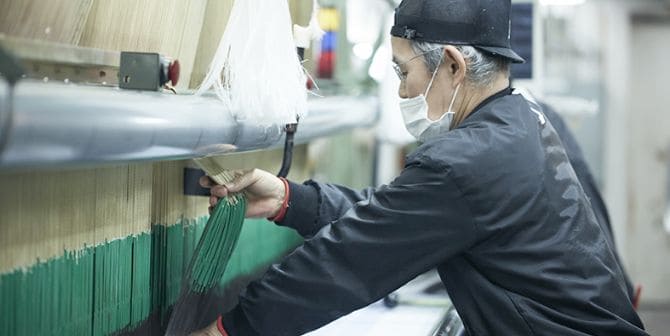
Weaving
The precision machine is set in motion by the skill and technique of the craftsman.
The new stretchers are put on the loom and joined with the yarns already on the loom. The approximately 3,000 to 5,000 threads are carefully combed and manually set in a machine called a tying machine to join them together, and finally the towel weaving process begins. In the factory, where the once famous TOYODA8 loom by Toyoda Automatic Loom and the latest high-speed looms are lined up, training is given to the younger generation on a daily basis in order to pass on the skilled techniques. After weaving is finished, the fabric rolls are unrolled so that they can be aired while checking for weaving defects and stains, and then moved to the dyeing factory.
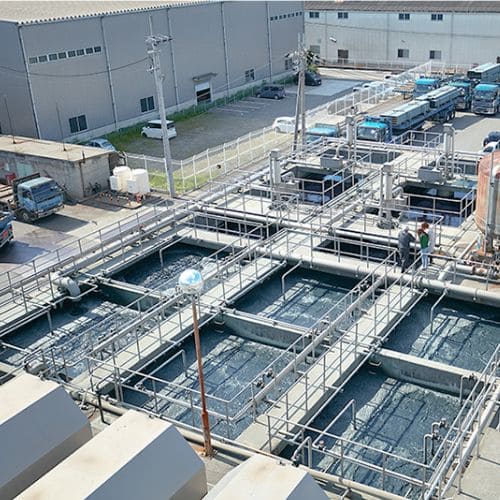
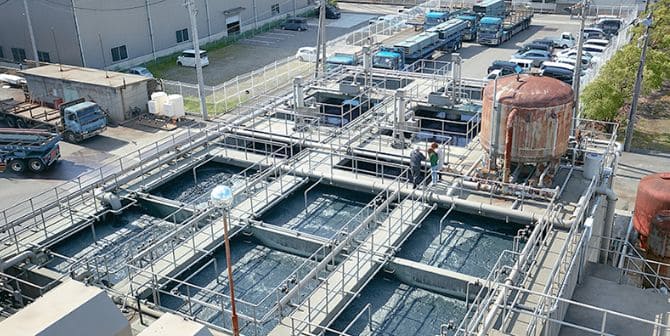
Desizing and Dyeing
Dyeing factory with the world's highest standard
Dyeing factory with wastewater purification facility
After the glue on the threads is washed away, the pure white fabric is dyed. Reactive dyes that do not contain heavy metals are used. Wastewater is the biggest environmental impact of using reactive dyes, but our wastewater purification facility with COD of 12ppm or less meets the strict standards of the Seto Inland Sea.
After dyeing and washing using plenty of virgin water from the Ishizuchi Mountains, the highest mountain range in western Japan, the fabric is put through a dryer to give it a firm texture with a pile that stands up.
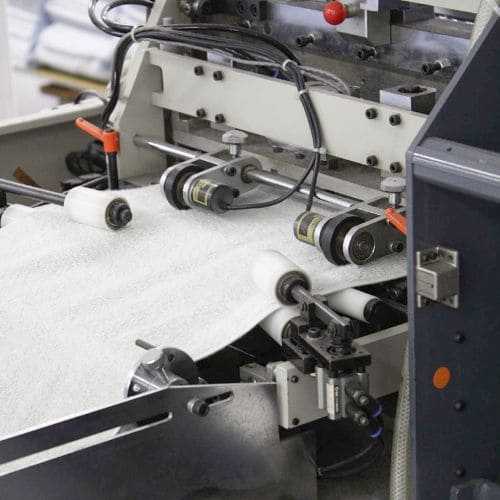
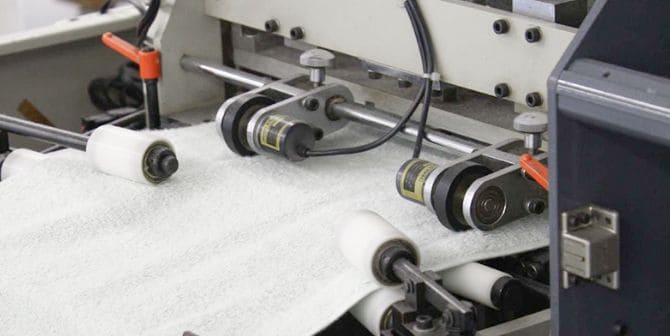
Ear wrapping and hemming
Each piece of fabric is
carefully made by hand.
Towel fabrics are cut one row at a time by a machine called a slitter. The ends are then sewn by a sewing machine, and each piece is cut by hand. The yellow IKEUCHI ORGANIC name is also sewn in this process.
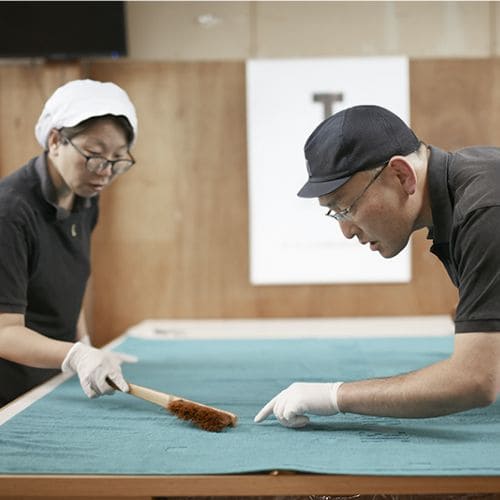
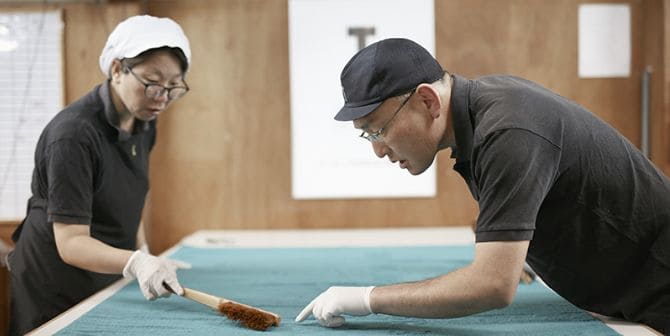
Inspection and shipping
Final checks are made by human eyes and hands.
Each finished towel is inspected according to strict standards. We carefully inspect each towel for weaving defects, missing piles, stains, and deformation. Only towels that meet these standards are shipped from the factory as IKEUCHI ORGANIC towels.